Precision Parts Cleaning Systems
Cleaning Methods Used in Precision Parts Cleaning Systems
This cleaning technique utilizes chemical solutions or solvents to dissolve or remove contaminants from surfaces. Various chemicals and formulations may be used depending on the type of contamination present and the material being cleaned.
Ultrasonic Cleaning: Ultrasonic cleaning uses high-frequency sound waves that typically range from 20-200kHz to create microscopic bubbles in the liquid cleaning solution. The implosion of these bubbles produces intense cleaning action which dislodges surface contaminants.
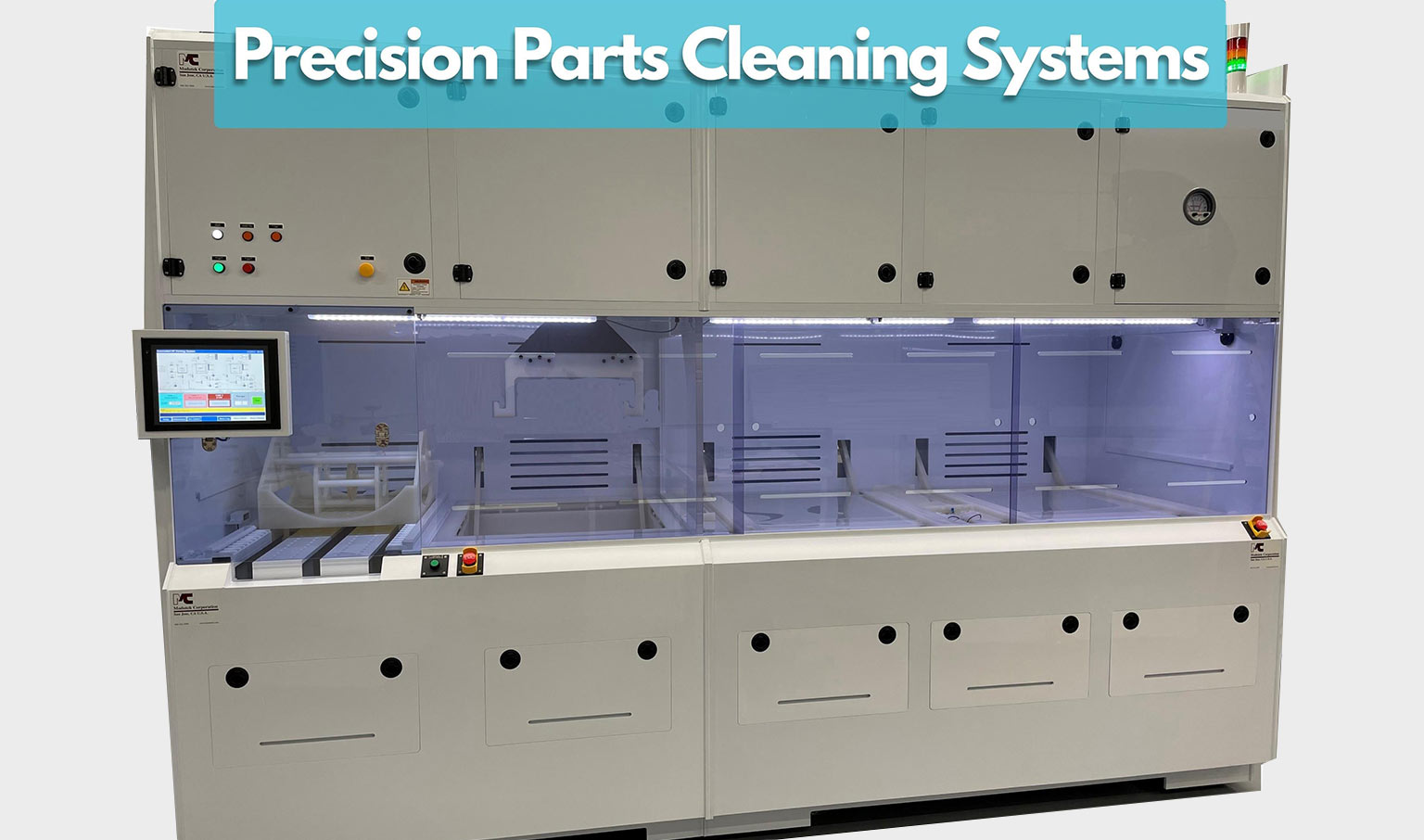
Megasonic Cleaning
Megasonic cleaning is similar to ultrasonic cleaning but operates at much higher frequencies, typically at or above 1.0MHz. It is highly effective at removing sub-micron particles during the manufacturing process of semiconductors, MEMs, and solar panels and can be used for delicate parts.
Cleaning Equipment
Batch Cleaners: For precision parts cleaning systems, batch cleaners are an invaluable asset. They consist of tanks or chambers where parts can be immersed in cleaning solutions or exposed to processes like ultrasonic and megasonic agitation. Batch cleaners provide effective cleaning capabilities while accommodating various part sizes and shapes.
Automated cleaning systems integrate various cleaning processes, handling, and drying steps within a single system. They are used in high-volume production environments and provide consistent cleaning results.
Cleanroom Environment
Precision parts cleaning systems are used in the semiconductor industry in a controlled cleanroom environment to minimize contamination. Cleanrooms have stringent air quality standards that include humidity, temperature, and particulate control to help eliminate potential sources of contamination during cleaning processes.
Contamination Control
Contamination control is critically important in precision parts cleaning. Below are some considerations regarding its implementation:
Part Handling: Proper handling techniques that prevent operator contamination include gloves and cleanroom-compatible tools when handling components.
Cleaning Solutions and Chemicals: Selecting appropriate cleaning solutions and chemicals is essential to efficiently eliminate contaminants without damaging parts.
Filtration: Filtration systems remove particles or impurities from cleaning solutions to provide consistent performance.
Drying: After cleaning, parts must be dried thoroughly to avoid watermarks and accumulation of residues. Spin drying or low-contamination drying techniques may be used.
Quality Control
Quality control measures should be implemented to verify the effectiveness of a cleaning process. This can include visual inspections, cleanliness testing using techniques such as particle counting or surface analysis, and validation of process parameters.
Specific cleaning processes and requirements vary based on the type of precision parts, contamination sources, and semiconductor manufacturing processes involved. Modutek works directly with customers to ensure their precision parts cleaning systems are designed to meet the specific cleaning procedures needed for each customer’s unique process requirements.
- Benefits
- Features
Benefits
- Handling capabilities from 1-500lbs.
- Capable of handling all parts of any shape and size
- Designed around your exact specifications
- A long-established history of parts cleaning
- Designed specifically for your cleanroom facility
- Multiple automation robot options available
- Recipes and repeatable through automation
- Multiple tank sequencing to improve throughput
- Data logging or interfacing with your host software
- Barcode and RFID part tracking available
- UL or NRTL third-party certification available
Features
- FM4910 construction material
- Available in any size and length to meet your requirement
- All stations wired per NFPA 70 & 79
- PCL with touch screen/GUI (graphic user interface)
- Servo motor motors with encoder feedback
- Emergency Power Off (EPO) with mushroom button and all safety interlocks
- All process tanks with 1” lip exhaust
- N2 head case purge with interlock
- Photohelic with interlock to EPO
- PVC safety shields
- Teflon N2 gun and DI water hand spray
- Continuous flow DI water manifold
- Casters and leg levelers
- One-year warranty on all parts
- Benefits
- Features
Benefits
- Handling capabilities from 1-500lbs.
- Capable of handling all parts of any shape and size
- Designed around your exact specifications
- A long-established history of parts cleaning
- Designed specifically for your cleanroom facility
- Multiple automation robot options available
- Recipes and repeatable through automation
- Multiple tank sequencing to improve throughput
- Data logging or interfacing with your host software
- Barcode and RFID part tracking available
- UL or NRTL third-party certification available
Features
- FM4910 construction material
- Available in any size and length to meet your requirement
- All stations wired per NFPA 70 & 79
- PCL with touch screen/GUI (graphic user interface)
- Servo motor motors with encoder feedback
- Emergency Power Off (EPO) with mushroom button and all safety interlocks
- All process tanks with 1” lip exhaust
- N2 head case purge with interlock
- Photohelic with interlock to EPO
- PVC safety shields
- Teflon N2 gun and DI water hand spray
- Continuous flow DI water manifold
- Casters and leg levelers
- One-year warranty on all parts
Benefits
- Handling capabilities from 1-500lbs.
- Capable of handling all parts of any shape and size
- Designed around your exact specifications
- A long-established history of parts cleaning
- Designed specifically for your cleanroom facility
- Multiple automation robot options available
- Recipes and repeatable through automation
- Multiple tank sequencing to improve throughput
- Data logging or interfacing with your host software
- Barcode and RFID part tracking available
- UL or NRTL third-party certification available
Features
- FM4910 construction material
- Available in any size and length to meet your requirement
- All stations wired per NFPA 70 & 79
- PCL with touch screen/GUI (graphic user interface)
- Servo motor motors with encoder feedback
- Emergency Power Off (EPO) with mushroom button and all safety interlocks
- All process tanks with 1” lip exhaust
- N2 head case purge with interlock
- Photohelic with interlock to EPO
- PVC safety shields
- Teflon N2 gun and DI water hand spray
- Continuous flow DI water manifold
- Casters and leg levelers
- One-year warranty on all parts
Contact our team to discuss your precision parts cleaning requirements.